一个充满挑战又让客户非常满意的项目
丰田汽车位于法国北部昂奈(Onnaing)的工厂,每天生产多达1200辆丰田雅力士(Yaris),精细的生产流程,让每一秒都得以充分利用。 2019年9月,该工厂安装了AP&T线尾码垛自动化设备,来快速高效地处理成形金属零件。而在短短一年的运转后,再次验证,设备完全达到了丰田公司所有的期望与要求。
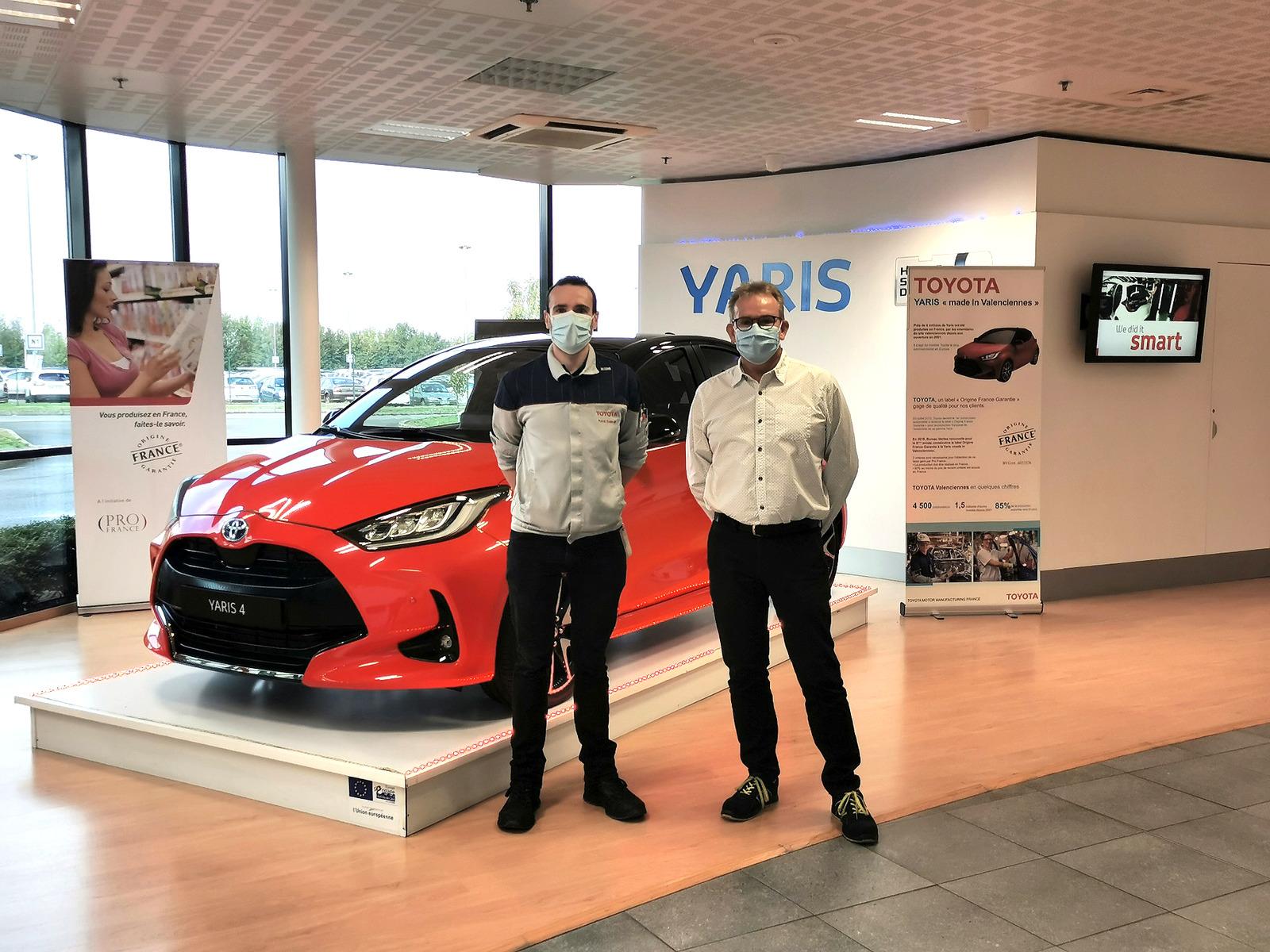
在2016年欧洲钣金展(EuroBLECH)上的一次邂逅,丰田公司便对AP&T公司产生了兴趣。
“当时我们正在为一个项目寻找欧洲合作伙伴,AP&T先进且机械设计简洁的产品吸引了我们,因此三年后我们在工厂里安装了这套高效的线尾系统”,法国丰田汽车公司车身部门的项目经理Rémi Delimal说道。
该设备包括一个从现有多工位产线接收零件的穿梭系统和一个带伺服驱动夹具的快速机械手便于在不同产品之间进行全自动切换。快速机械手从穿梭机上夹拾零件,并将其堆放在全自动托盘系统中。该设备交付还包含了与已有产线的集成。压力机以25冲程/分钟的速度运行,甚至以23冲程/分钟的速度进行一冲双件生产,这样的生产节拍对设备的要求极高。
“这么高速的情况下,单独移动每个零件都非常困难。于是,我们设计了解决方案:先将若干零件码在一个夹具中,然后再下一个动作时全部送入料站。而循环周期时间则不允许超过下次堆满夹具的时间,”AP&T大客户经理Peter Karlsson说道。
循环周期时间短并不是该项目的唯一难点;由于在该产线上将生产超过30种不同的零件,在产品切换时必须做到快速换夹手,而每次的更换时间不能超过180秒。
“为了解决这个问题,我们采取了使用单个夹手对应不同零件产品的方式,来替代更换换夹手的操作,操作人员可以简单的通过在操作面板上更换不同产品的程序(与产品配方相关联)来实现,这样不仅简化了工艺,而且明显缩短了产品切换的时间”, Peter Karlsson继续说道。
对于AP&T,这不仅是要达到丰田对设备性能的高要求,也要达到对安装本身的高要求。
“对我们来说,设备必须在工厂下班时进行安装,以免影响正常生产;而且我们只有三周时间将自动化设备安装到位,并将其集成到我们现有的压力机生产线中。这一切都进展顺利,按期完工。该设备一经交付,第一天起就投产使用了,其生产率和可靠性超出了我们的预期。这是我们合作的第一个项目,我们非常满意:从解决方案设计到安装调试服务、备件和技术支持,AP&T做得很好!”Rémi Delimal说。
“为世界上最大的汽车制造商提供设备,是AP&T迈出的重要一步。这意味着新的机遇,并进一步加强了我们在汽车工业的地位。” Peter Karlsson表示。
2020年11月
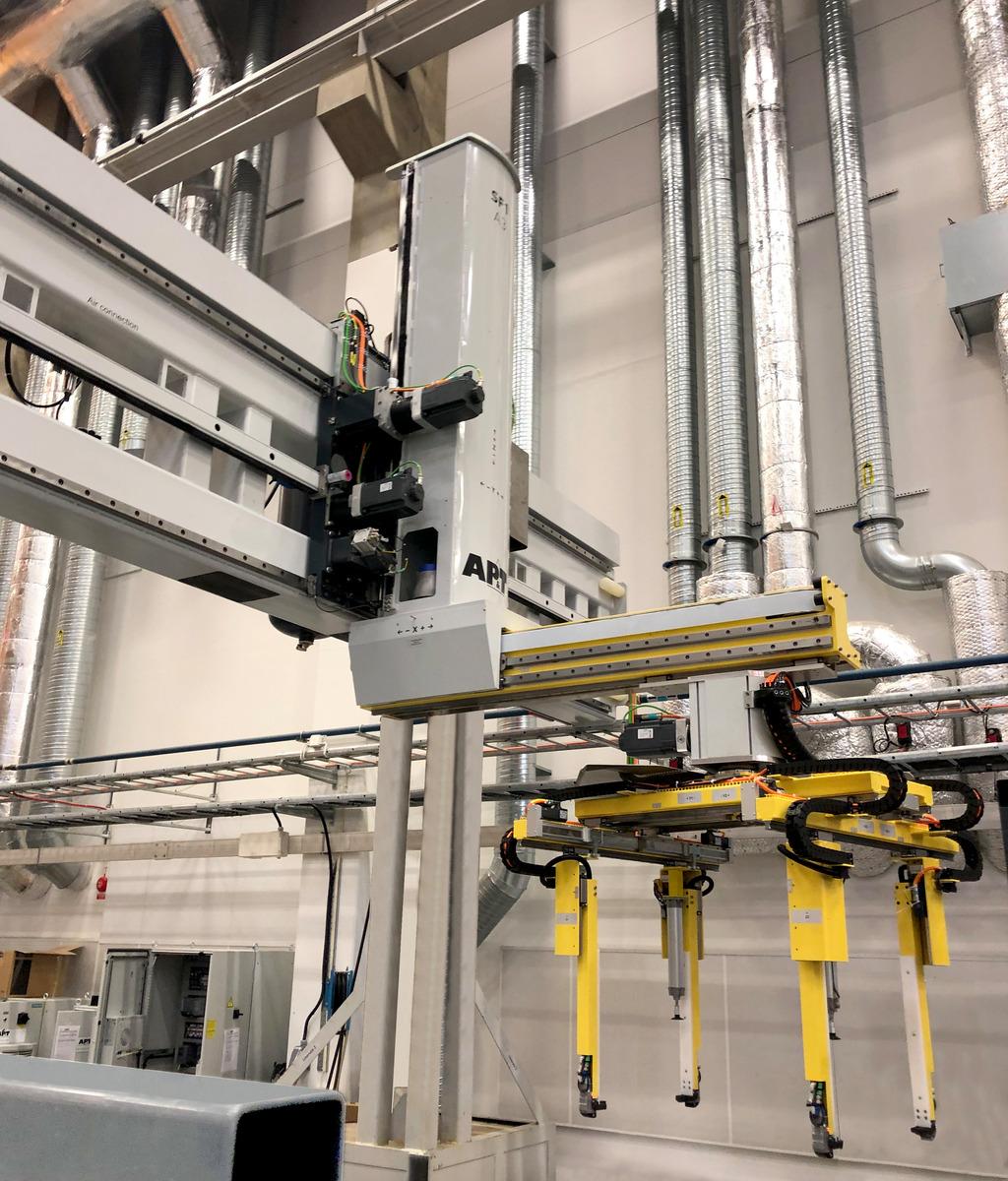
纪实
AP&T解决方案包含一个带特殊设计的夹具的四轴快速机械手和一个穿梭机/夹具解决方案,所有零件都是基于AP&T久经验证和标准化的模块化系统。
AP&T 高速码垛方案于2019年夏季在法国丰田工厂安装。