Toyota Motor Manufacturing France (TMMF)
Ein Projekt mit vielen Herausforderungen und einem, am Ende des Projekts, sehr zufriedenen Kunden
Die Toyota Produktionsanlage im nordfranzösischen Onnaing fertigt in einem außergewöhnlich schlanken Prozess, in dem jede Sekunde optimal genutzt wird, bis zu 1200 Toyota Yaris pro Tag. Im September 2019 wurde ein Abstapelsystem (End-of-Line-Lösung) von AP&T installiert, das eine schnelle und hocheffiziente Handhabung umgeformter Karosseriebauteile garantiert. Nach einem Jahr Produktion hat sich herausgestellt, dass das Equipment alle Erwartungen erfüllt hat.
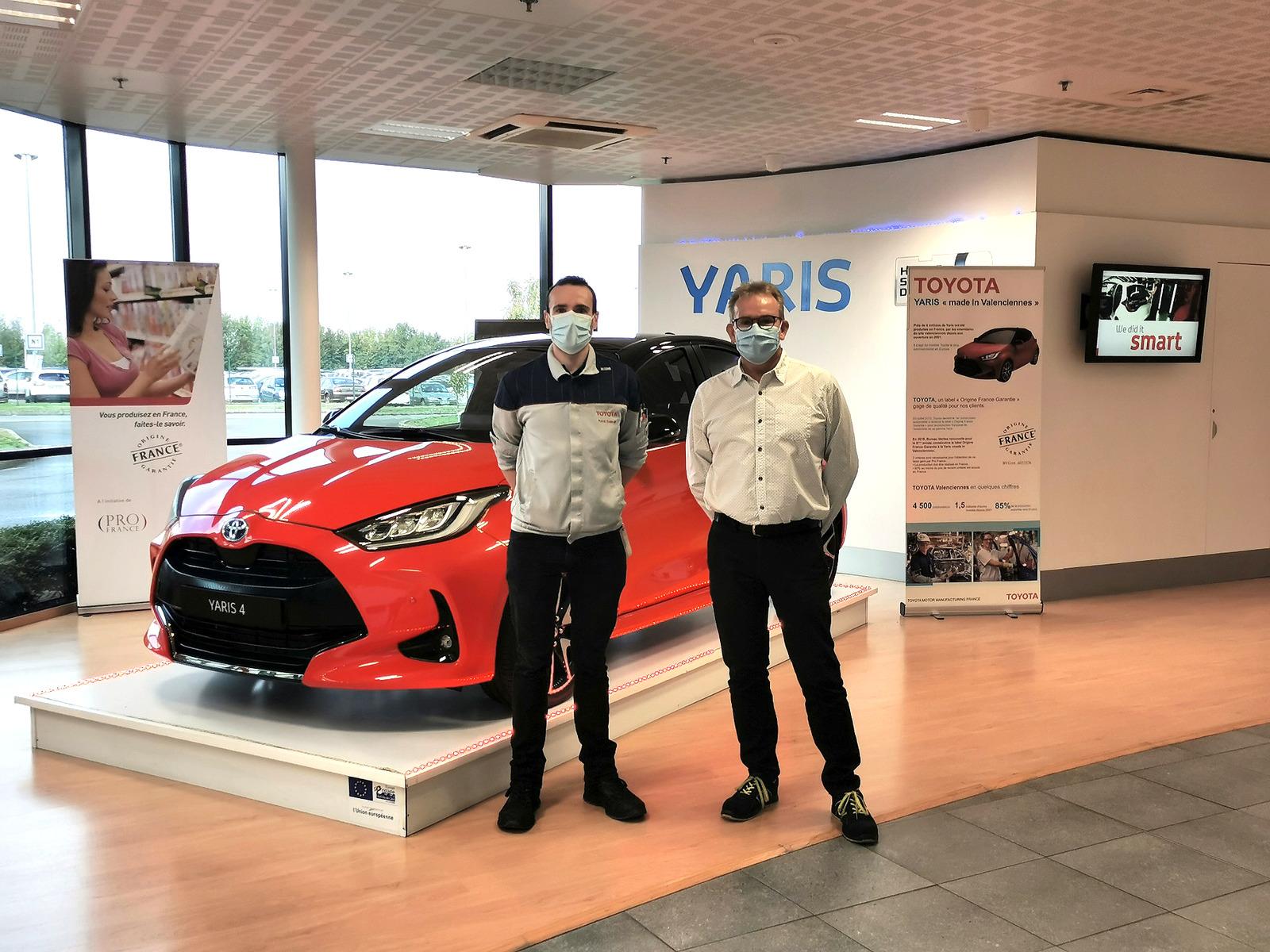
Nach der ersten Kontaktaufnahme zu AP&T auf der EuroBLECH 2016, war Toyota an AP&T interessiert.
„Wir waren auf der Suche nach einem europäischen Partner für dieses Projekt und die modernen, aber mechanisch unkomplizierten Produkte von AP&T waren für uns sehr attraktiv“, so Rémi Delimal, Project Manager bei TMMF, Press Shop, Body Division.
Und so wurde drei Jahre später ein Abstapelsystem (End-of-Line) installiert.
Das Equipment besteht aus einem Shuttle-System, dem von einer vorhandenen Transferlinie Teile zugeführt werden und einem SpeedFeeder mit servomotorisch angetriebenem Greifer, der sich bei einem Produktwechsel vollautomatisch umstellt. Der SpeedFeeder entnimmt die Bauteile aus dem Shuttle-System und stapelt sie in ein voll automatisiertes Palettensystem. Der Lieferumfang von AP&T umfasste auch eine Integration in die Linie und die Sicherheitsteuerung. Die Presse fährt mit einer Taktzahl von 25 Hübe/min und auch doppelt fallende Bauteile erreichen einen Takt von 23 Hübe/min. Die Zykluszeit stellt sehr hohe Anforderungen an das Equipment.
„Die hohe Geschwindigkeit ermöglicht es nicht, die Bauteile einzeln zu handhaben. Stattdessen werden mehrere Bauteile in einer Bauteilaufnahme übereinandergestapelt und dann in einem Schritt verfahren. Der gesamte Zyklus darf nicht mehr Zeit in Anspruch nehmen, als für das Auffüllen der Bauteilaufnahme erforderlich ist“, erklärt Peter Karlsson, Key Account Manager bei AP&T.
Die kurze Zykluszeit ist jedoch nicht die einzige Herausforderung die uns im Zusammenhang mit dem Projekt gestellt wurde. Über 30 verschiedene Teile werden in der Transferlinie gefertigt und die Umstellung von einem Produkt auf ein anderes muss schnell erfolgen. Ein Greiferwechsel darf nicht länger als 180 Sekunden dauern.
„Wir lösten das Problem sehr simpel, indem wir nur ein Greifersystem für alle Produkte verwenden. Statt einen physischen Greiferwechsel durchzuführen, kann der Bediener die Programme für die verschiedenen Produkte über die HMI anwählen (abhängig vom jeweiligen Produktprogramm), was den Prozess vereinfacht und den Rüstprozess des Kunden erheblich verkürzt“, sagt Peter Karlsson.
AP&T ging es nicht nur darum, die hohen Anforderungen zu erfüllen, die Toyota an die Leistung des Equipments stellt, sondern auch die hohen Anforderungen an die Installation selbst.
„Für uns war es das Wichtigste, dass die Installation durchgeführt wird, während das Werk geschlossen ist, so dass die Produktion davon nicht beeinträchtigt wird. Uns standen nur drei Wochen zur Verfügung, um das Automatisierungssystem zu installieren und in unsere vorhandene Pressenlinie zu integrieren. Alles lief reibungslos und wir waren fertig, nach dem vorgegebenen Terminplan. Das Equipment hat ab dem ersten Tag der Produktion geliefert und unsere Erwartungen an die Produktivität und Zuverlässigkeit übertroffen. Das war unser erstes gemeinsames Projekt und ich muss sagen, dass AP&T gute Arbeit geleistet hat. Angefangen bei der Lösungskonzeption bis hin zur Unterstützung, die wir in Form von Service, Ersatzteilen und technischem Support erhalten“, erklärt Rémi Delimal.
„Das Vertrauen zur Lieferung von Equipment von einem der größten Automobilhersteller der Welt zu erhalten, ist für AP&T ein wichtiger Schritt. Das bedeutet neue Möglichkeiten und stärkt gleichzeitig unsere Position in der Automobilindustrie“, sagt Peter Karlsson.
Dezember 2020
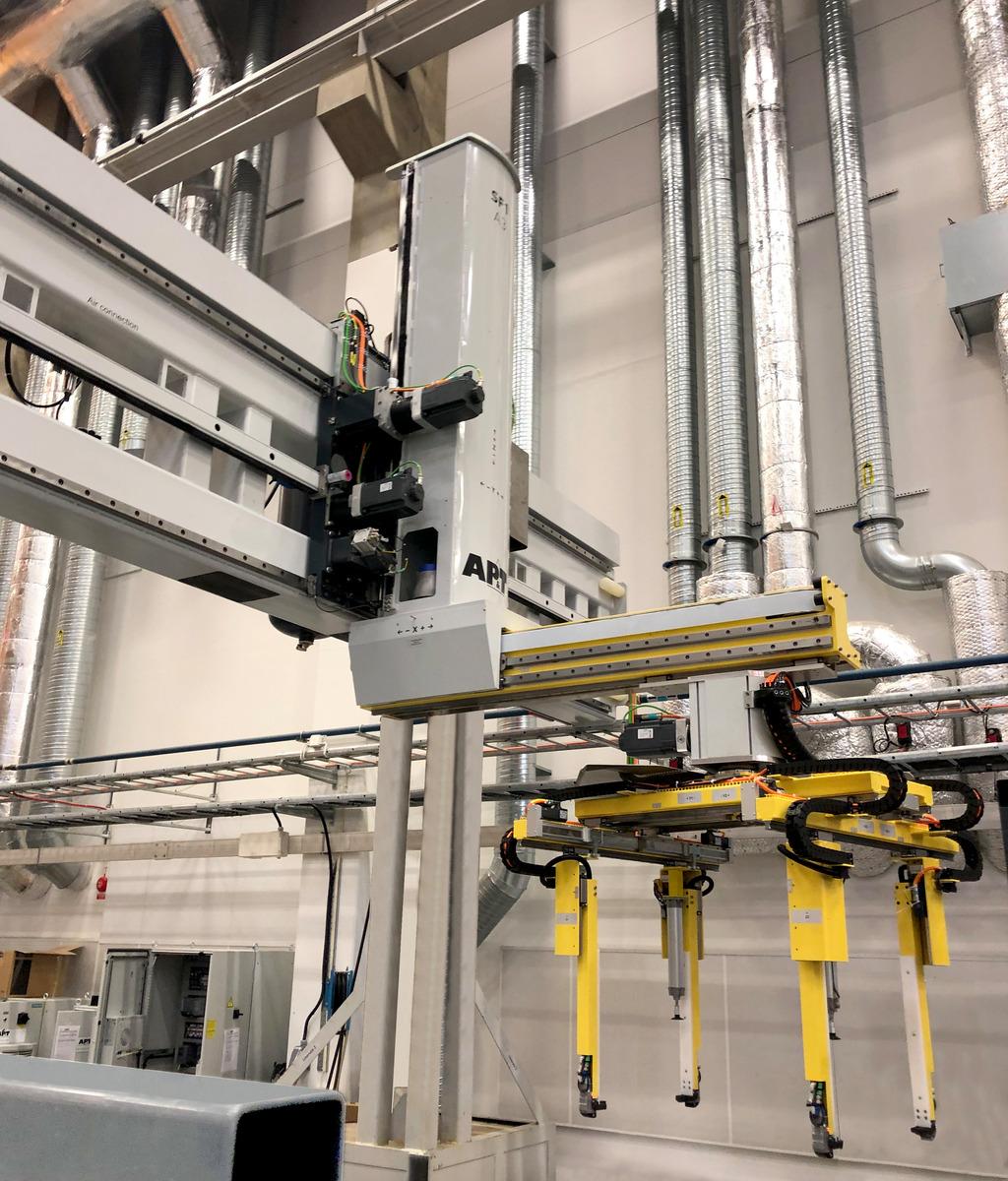
Fakten
Die Lösung von AP&T umfasst einen vierachsigen SpeedFeeder Pressenroboter mit einem speziell konzipierten Greifer und eine Shuttle-Bauteilaufnahme-Kombination. Alle Komponenten basieren auf dem bewährten und standardisierten modularen System von AP&T.
Die neue „End-of-Line“-Lösung von AP&T wurde im Spätsommer 2019 in der Produktionsanlage von Toyota installiert.