Development Areas
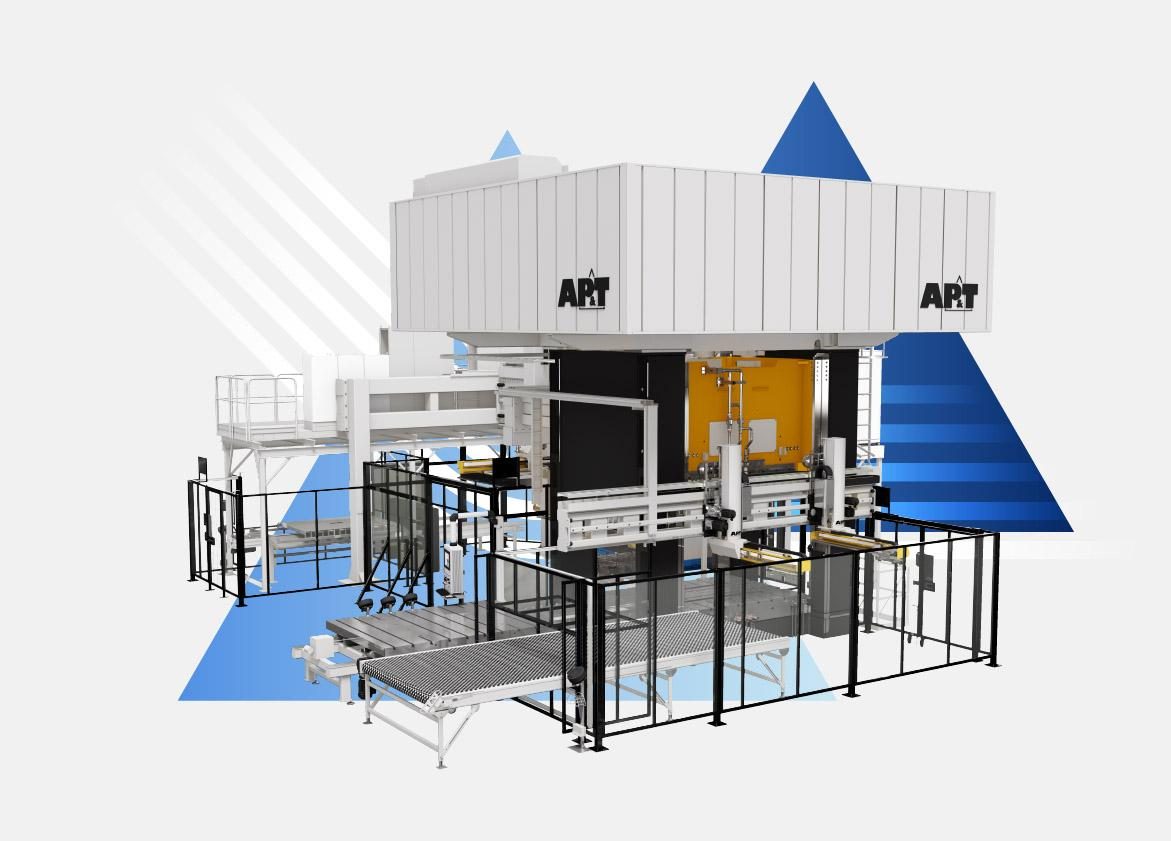
Line Development
Line Development develops products, standards and methods for AP&T’s production lines, with a strong focus on customer productivity. Production lines from AP&T are used in a wide range of industries and application areas, from forming of high-strength aluminum within the automotive industry to standard solutions for pressing sheet metal parts for roof drainage systems. In order to meet the specific needs within each area, we work in a cross functional and integrated way with all of the product groups at AP&T and with selected customers. Doing so allows us to continuously improve the overall performance, user friendliness and reliability of the lines. One way in particular we achieve this improvement is by utilizing the potential found in Industry 4.0. One related development project has resulted in new ways to control and optimize production lines and processes, as well as tools to calculate the total cost of ownership.
Automation Development
A large part of AP&T’s development work within automation is focused on creating new ways for customers to streamline their production and fully utilize Industry 4.0’s potential. Using AP&T’s flexible, modular-based program of linear robots as the foundation, we develop fully automated, connected machines that enable increased production speed, more consistent flows, greater reliability and lower energy consumption. At the same time, we continue to develop and refine our existing products’ qualities. AP&T’s development work comprises mechanics as well as electronics and software, and is conducted in close collaboration with customers and other stakeholders within various segments to ensure that a broad range of specific needs can be satisfied.
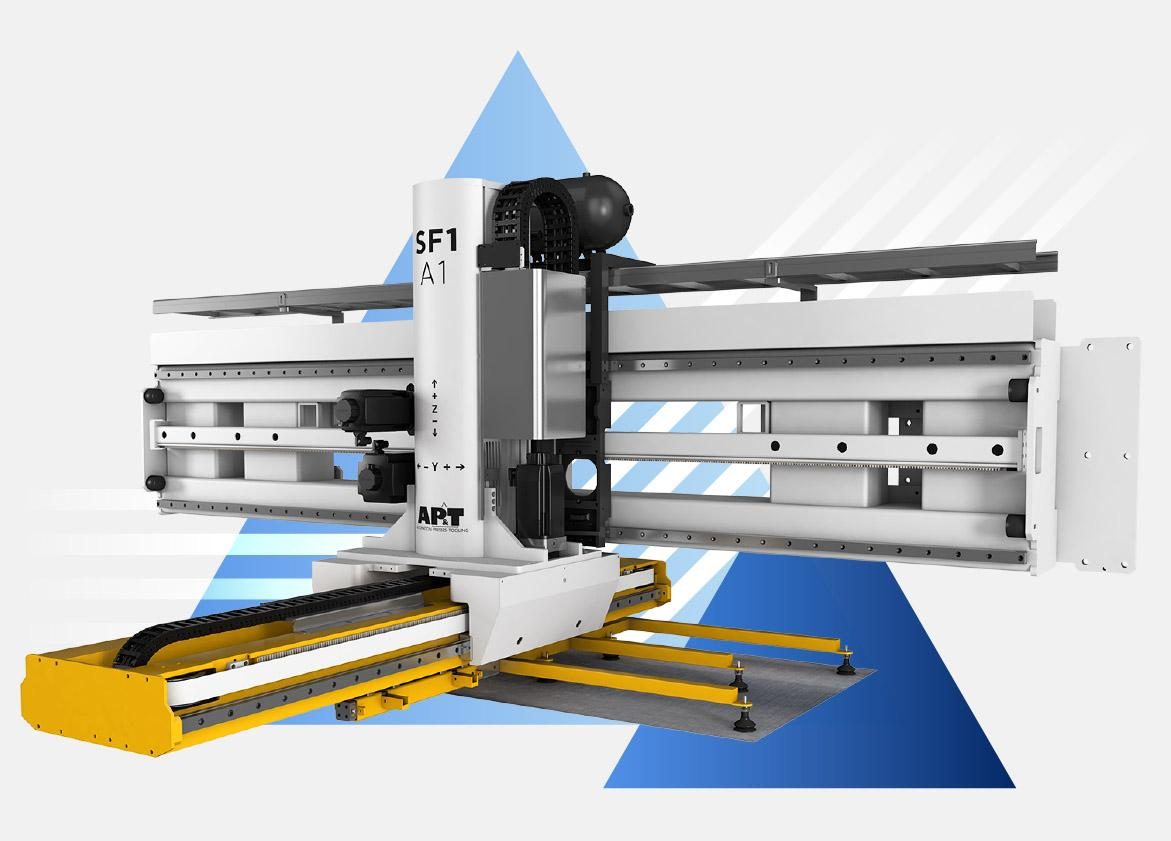
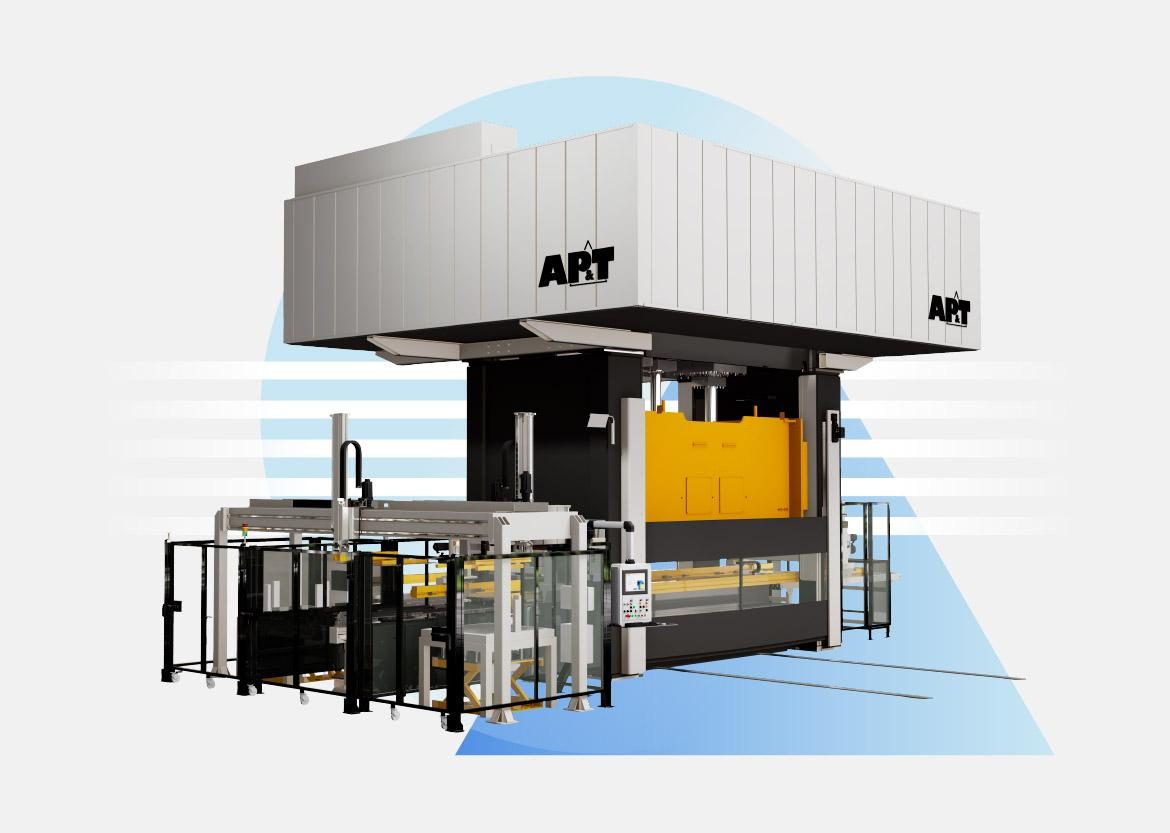
Press Development
The press development area develops complete presses and modules for both presses and tool changing systems. Among other things, development in the area has resulted in AP&T’s unique variable speed servo hydraulic press technology, whose combination of high performance, high energy efficiency and high flexibility addresses both current and future customer needs. The press development area is strongly focused on IoT-related solutions such as virtual commissioning, press and process monitoring, and predictive maintenance. Tools such as FEA for structural simulations, CFD and hydraulic simulation, together with R&D’s test presses, are used to verify our solutions at an early stage. We cooperate with customers and/or other functions within AP&T in a large number of our projects.
Furnace Development
The automotive industry’s need for flexible combinations of materials with low weight, high strength and good formability is driving the development of new methods and processes for heat treatment and hot forming. The furnace development area, in close cooperation with both car manufacturers and their subcontractors, produces industry-leading, modular-based solutions for press hardening of steel and hot forming of high-strength aluminum. AP&T’s Multi-Layer Furnace and TemperBox® are examples of innovations that have emerged from the company’s furnace development work.
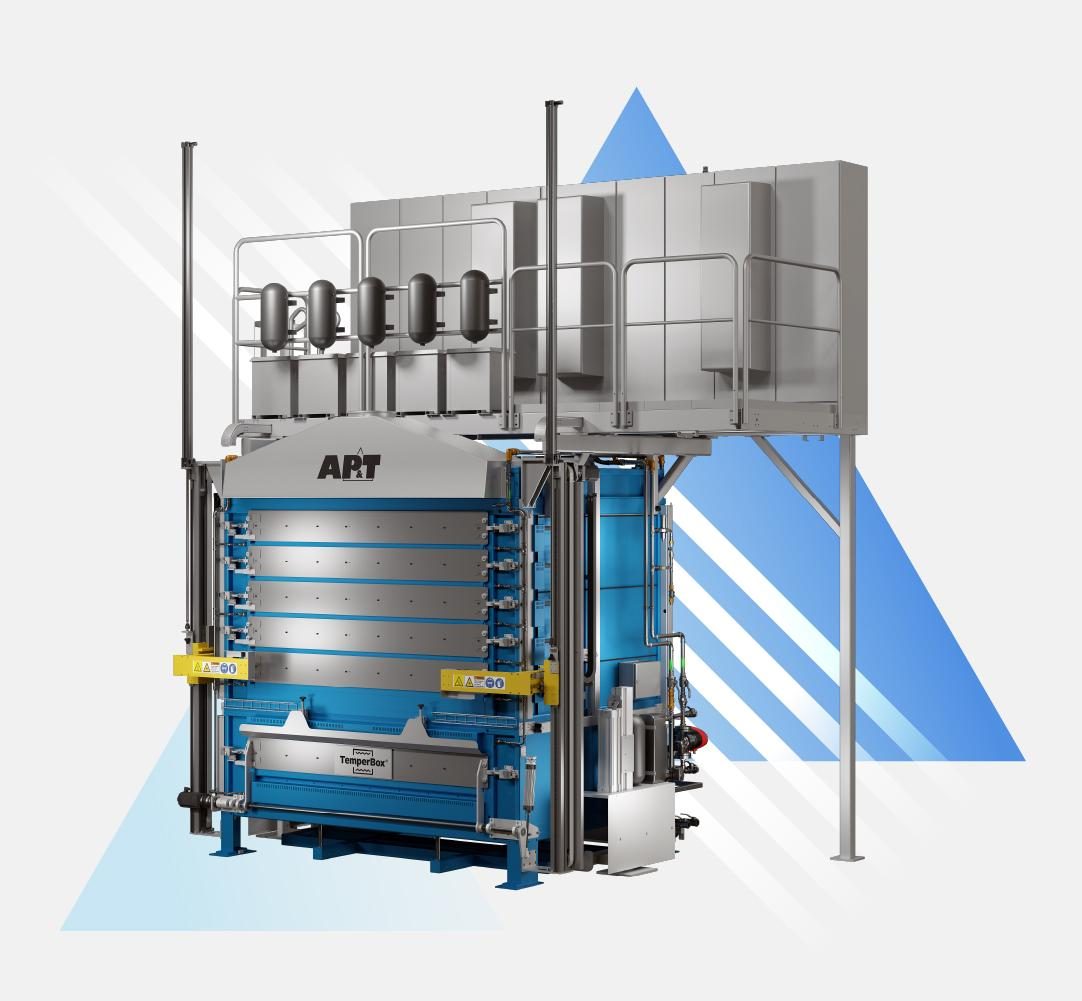
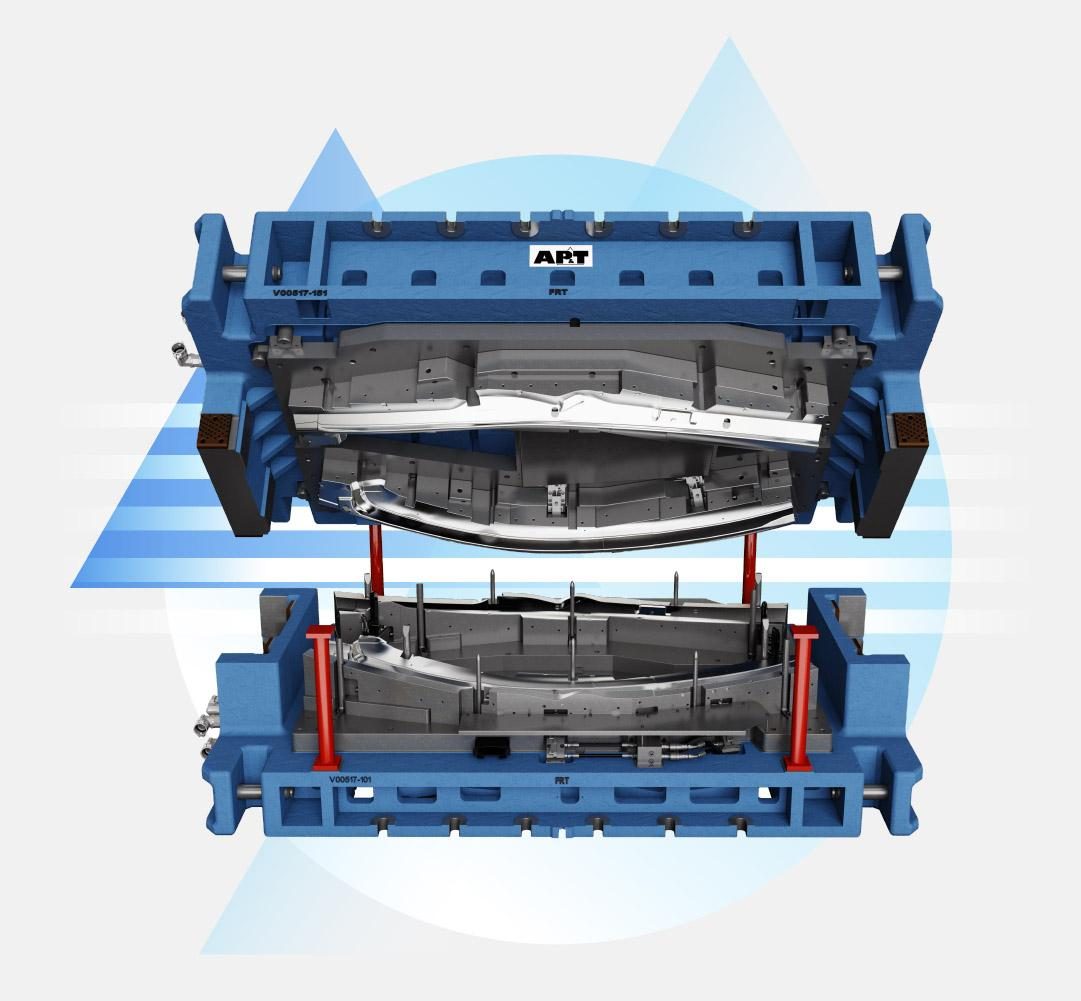
Tooling Development
AP&T’s tooling development area is focused on tribological challenges, such as finding ways to improve friction between blanks and forming tools using special coatings and different types of lubricants. FEM sheet forming simulations are calibrated and validated to evaluate forming behavior of new materials and to execute feasibility studies of future forming tools. We are also looking into new manufacturing methods for tooling, such as 3D printing and die casting. AP&T’s tooling development team cooperates with universities, research institutes and industry partners, and participates in many international and domestically funded projects. One of the area’s recent achievements was finding a solution for forming high-strength aluminum without the occurrence of adhesive wear (galling).
Forming Process Development
Investigating and developing manufacturing processes for new material concepts is the main task of AP&T’s forming process development area. Developing FEM sheet forming simulation models for new manufacturing processes is important in terms of enabling feasibility studies for tooling and determining the correct process parameters. Our work at present is mostly concentrated on processes for forming high-strength aluminum and composite materials. For example, we have optimized the process route for manufacturing high-strength aluminum components at a lower cost and with higher quality. This was achieved by investigating several different aging routes after the part is formed and quenched in the die. With the right aging route, process time can be reduced and joinability of high-strength aluminum can be increased. The impact on the washability of hot formed aluminum components when lubricants are applied was also investigated. We studied the performance of hot forming of high-strength aluminum when applied to chassis components, which are usually manufactured through bulk forming. The results are very promising.
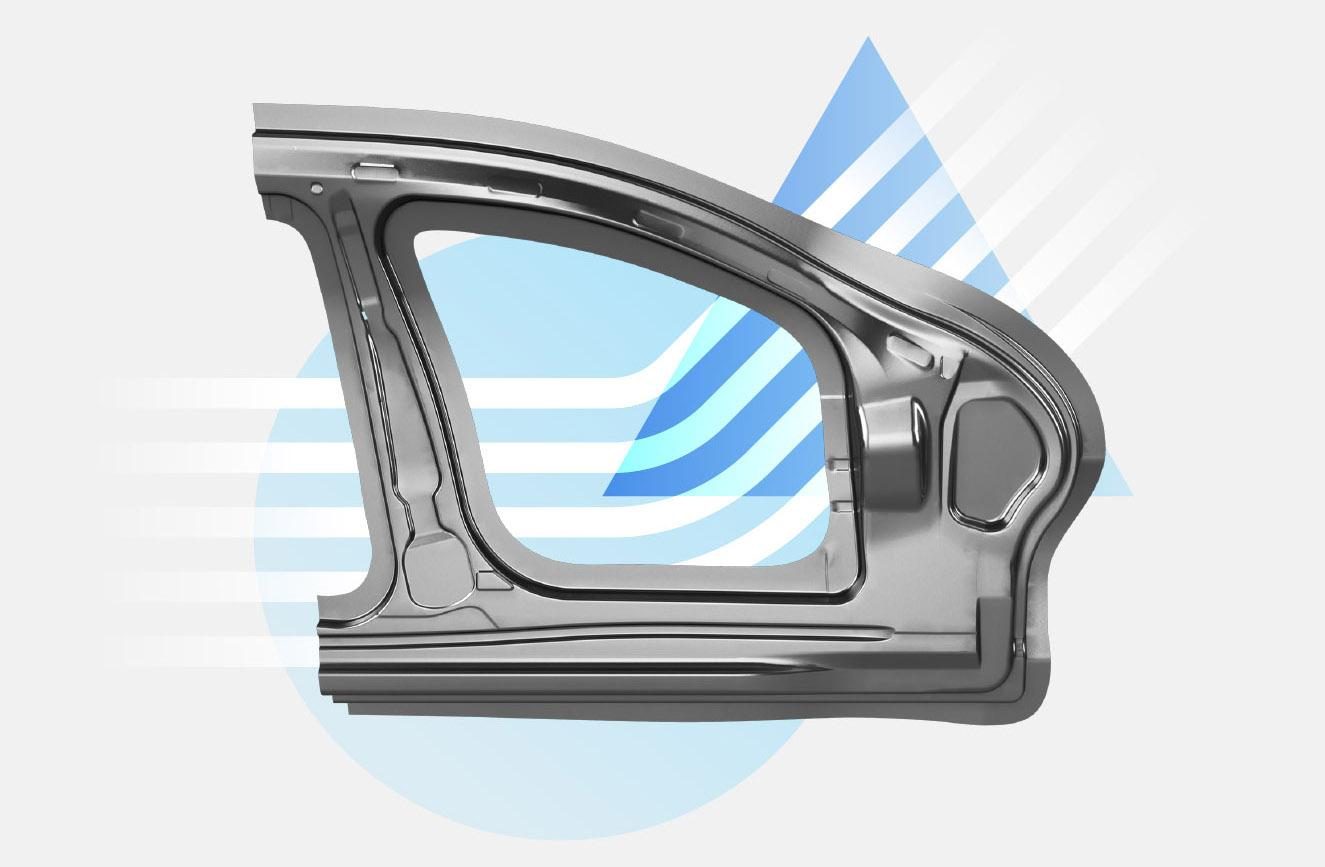
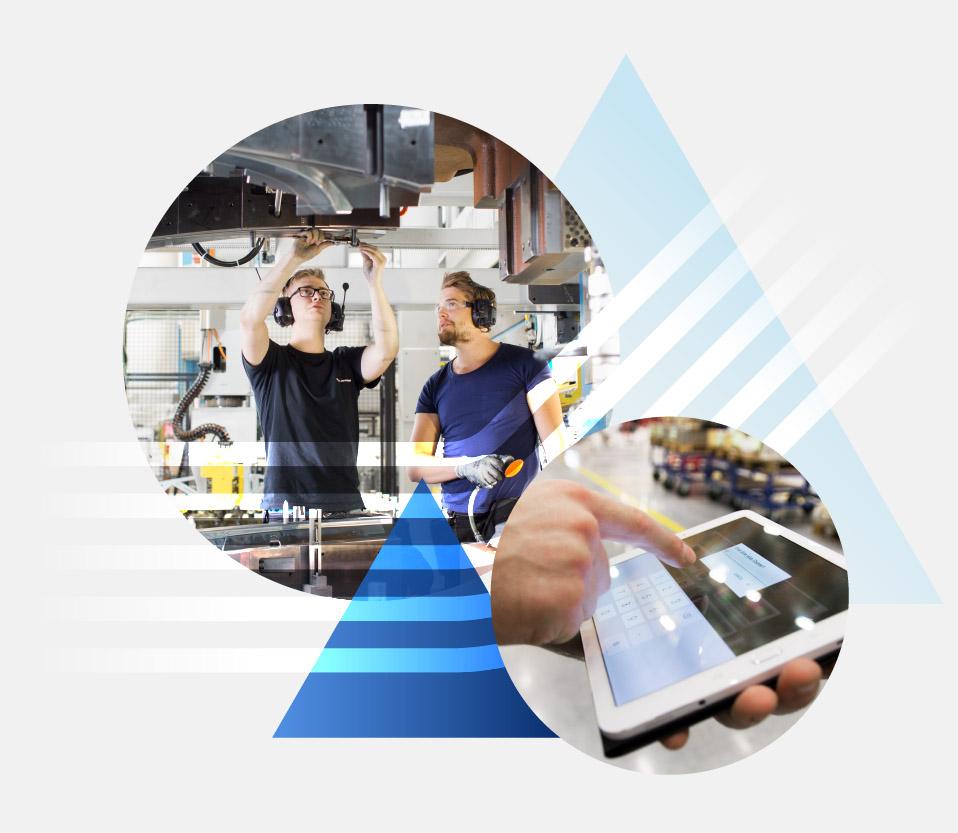
Aftermarket Services Development
With focus on customer productivity, AMS Development develops solutions that help ensure a high degree of availability and performance over the entire life cycle. In addition to methods for optimized and cost-efficient maintenance, we also develop connected software tools. The tools give both our service personnel and our customers access to machine and production data that make it easier to plan service, prevent stoppages and continuously improve the production process. Aftermarket products and services are developed in close cooperation with our product managers, customers and aftermarket organization.