AP&T gets more out of the Cassino factory press hardening lines
When Fiat Chrysler Automobiles (FCA) in Cassino, Italy invested in five complete press hardening lines from AP&T more than ten years ago, it wasn’t only AP&T's largest ever deal with a customer in the automotive industry at the time, it was also the start of an innovative, open-minded collaboration that paved the way for continuous optimization of manufacturing processes, shorter cycle times and increased productivity.
FCA's production facility in Cassino manufactures press hardened parts for a number of car models from the Group’s Alfa Romeo, Jeep and Fiat brands. AP&T delivered the press hardening lines between 2007 and 2008 and today, the lines have an even better production capacity than when they were installed. A main contributor to this is the preventive maintenance agreement that FCA and AP&T signed in the beginning of 2019.
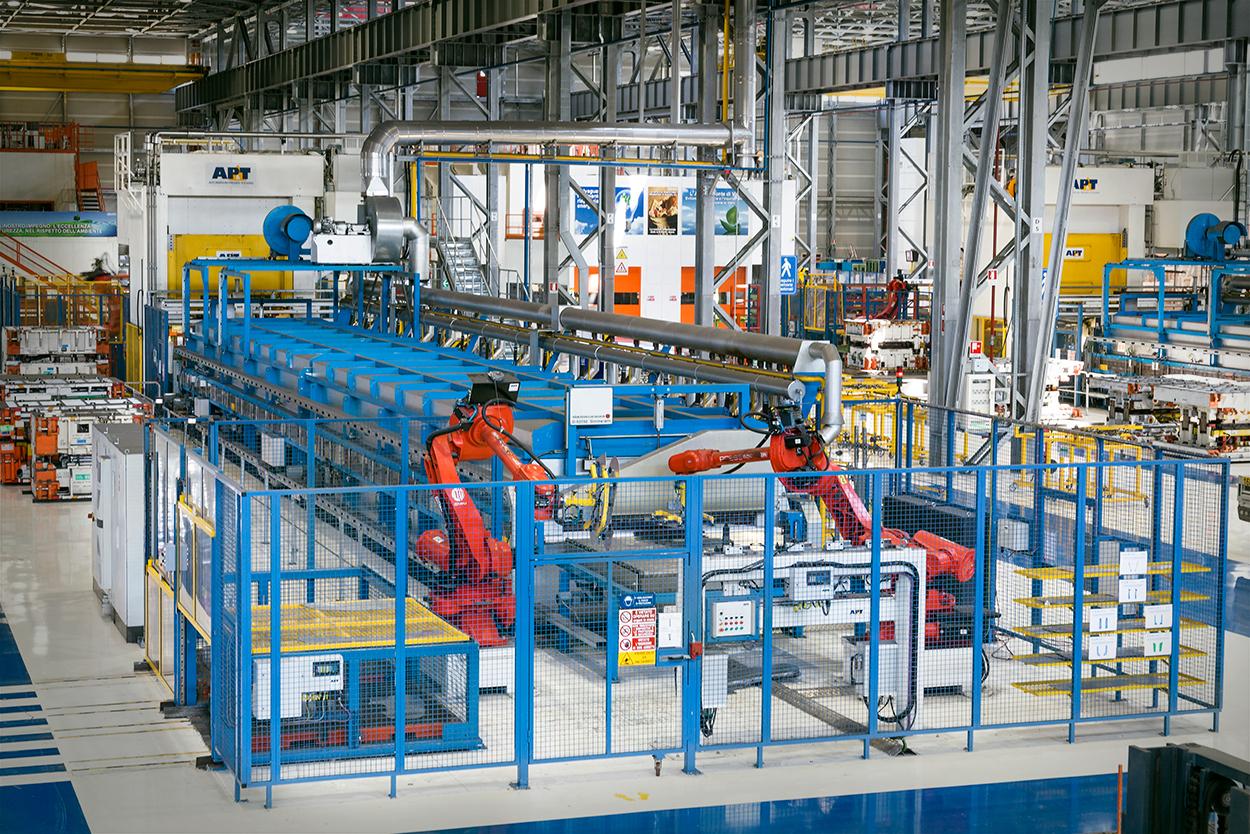
Needs-based availability agreement
“Technology is constantly developing and by upgrading and optimizing our customers’ existing equipment, we can improve performance while ensuring a long-term high level of operational reliability and availability. That’s why we initiated a discussion with Fiat, to learn how we could best accommodate their needs. Starting from the agreement levels that are included in our standard offer, we collaborated to create a customized maintenance and optimization solution for the Cassino factory press hardening lines,” Magnus Svenningsson, Director of Aftermarket Services at AP&T tells us.
“Machinery must be highly efficient for full saturation of hot stamping lines to be possible. This can be enabled by correctly using WCM methodology and by involving the manufacturer of the equipment. Thanks to their deep technical know-how, the manufacturer can detect weaknesses and propose technological improvements,” says Antonio Colucci, Head of the Press Shop and Dies Department in FCA EMEA.
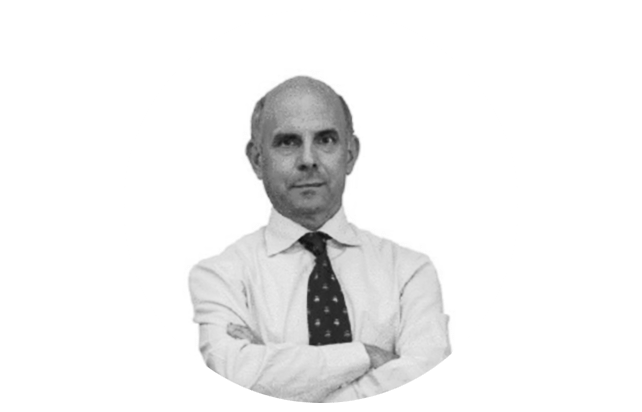
In addition to regular and security maintenance, technical feedback to the customer and optimization of machinery and systems, the agreement also includes advising the customer and giving suggestions for how productivity can be improved through new, innovative technology. The parties meet once a year to thoroughly review needs and opportunities.
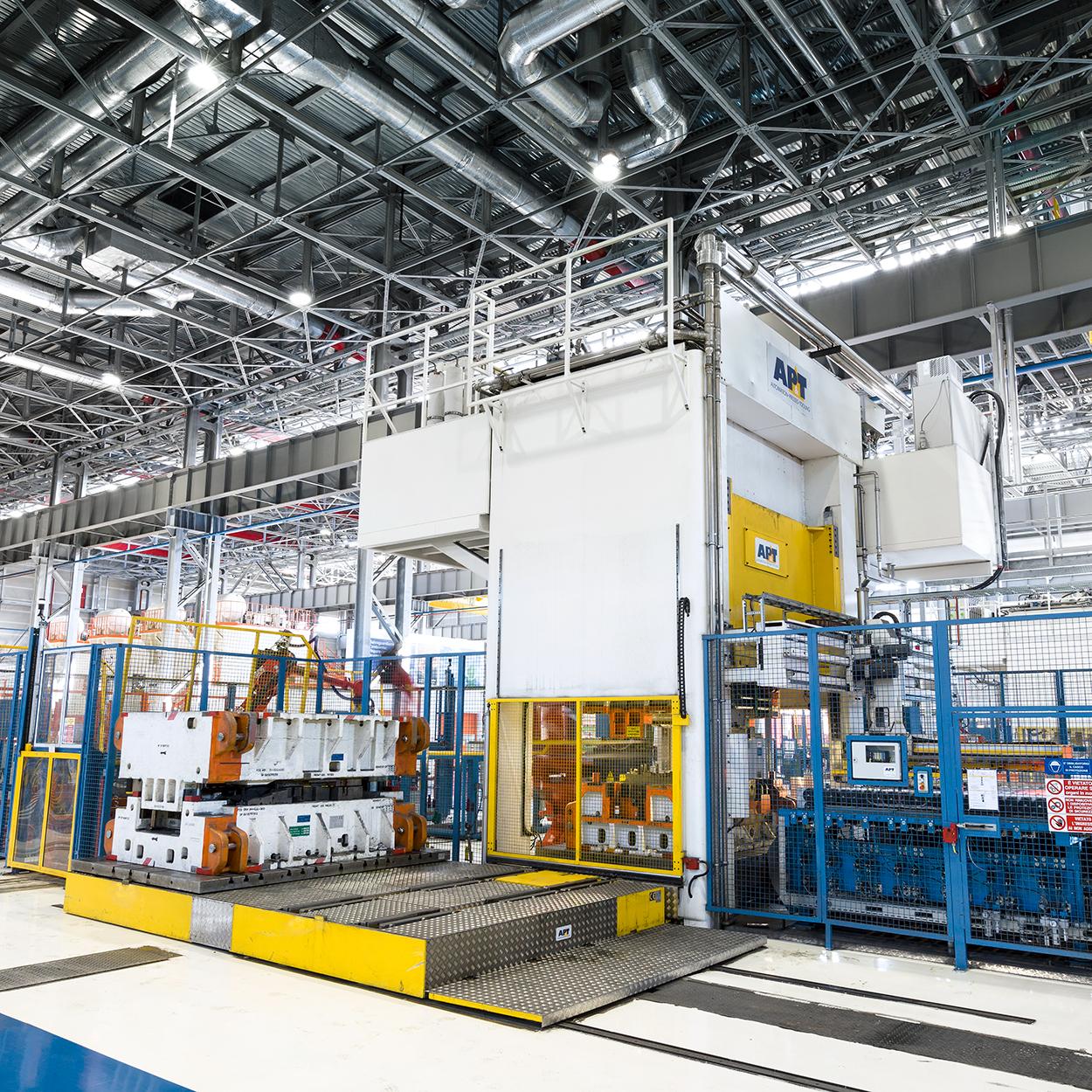
New cooling system resulted in shorter cycle times
“It is extremely advantageous that the same company that designed and manufactured the lines are also taking care of maintenance, optimizing functionality and informing us of interesting technological innovations that can contribute to short and long-term improvement. It is a fruitful collaboration that we are very pleased with,” says Cesare Zeppieri, Cassino Press Shop Operational Manager.
One example of an innovative solution that was implemented on the Cassino factory press hardening lines is the new cooling system for press tools, developed by AP&T. By optimizing the cooling system capacity, the cooling process is now much faster than before.
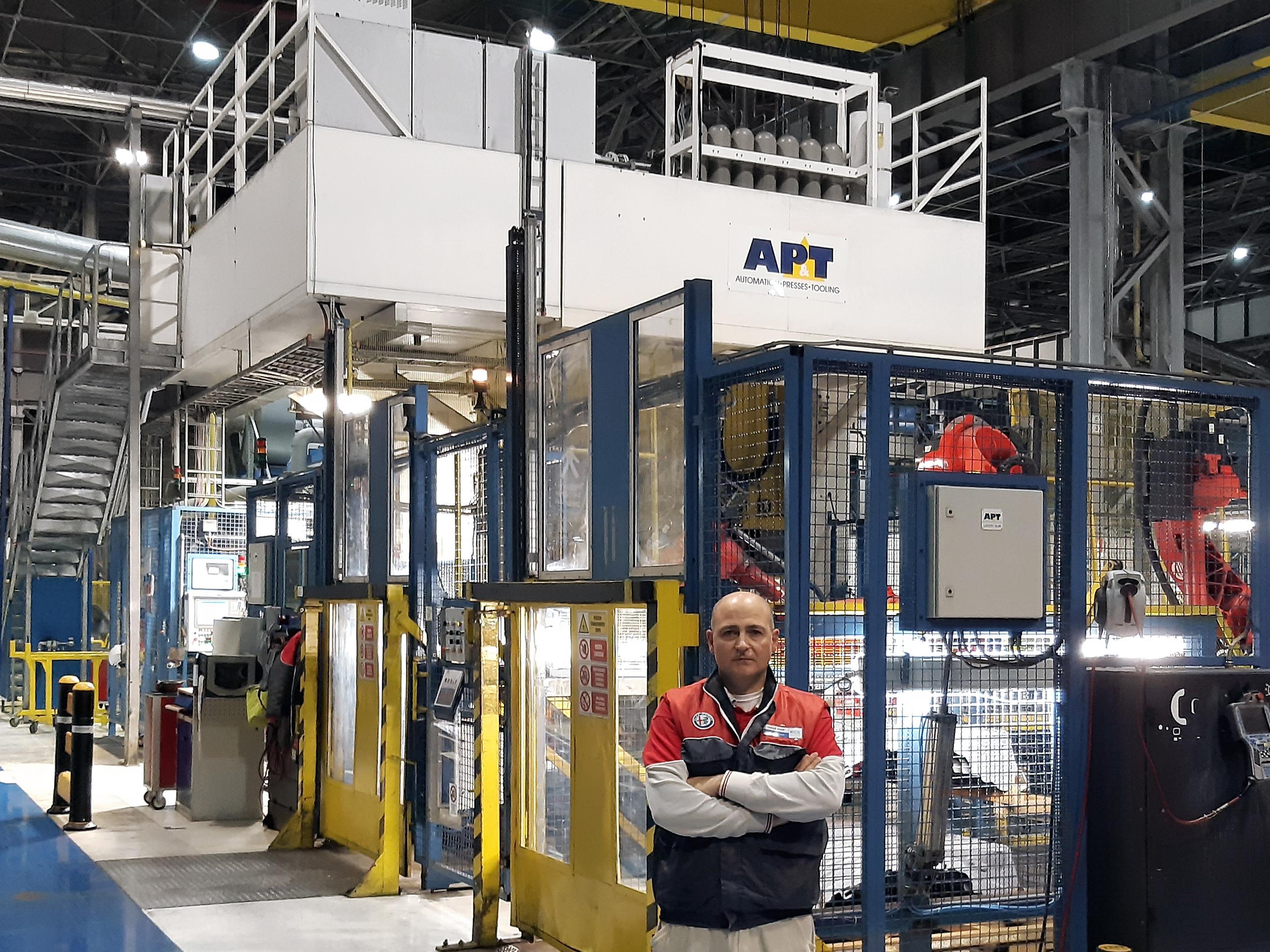
“It has meant substantially reduced cycle times, making it possible to form more parts in a shorter amount of time. All new tools brought into use, and many existing tools, utilize this type of cooling. Another solution we find highly interesting and are looking into is AP&T's in-line process monitoring. We’re also keeping an eye on how they develop the TemperBox® technology,” says Zeppieri.
AP&T's in-line process monitoring provides full control over heating and cooling by using infrared camera technology and a pyrometer, making it easier to ensure that each part lives up to the quality requirements. TemperBox® makes it possible to manufacture press hardened parts with both hard and soft zones in the same process.
Service and maintenance provide high availability
“Though we are already having an interesting discussion about what we will be able to accomplish in the future with new technology, it behooves us to remember the importance of the continuous support we provide through our qualified support, professional maintenance and our well-oiled spare parts supply. That’s what lays the foundation for the high availability of the lines,” says Magnus Svenningsson.
“Naturally, we strive to have the shortest, best planned downtime possible. AP&T’s service technicians know what we need, are always well-prepared and do their jobs in a timely manner. And a gold star also goes to spare parts supply. They're quick. The parts we need are always in stock and are delivered within 24 hours,” says Cesare Zeppieri.
March 2021
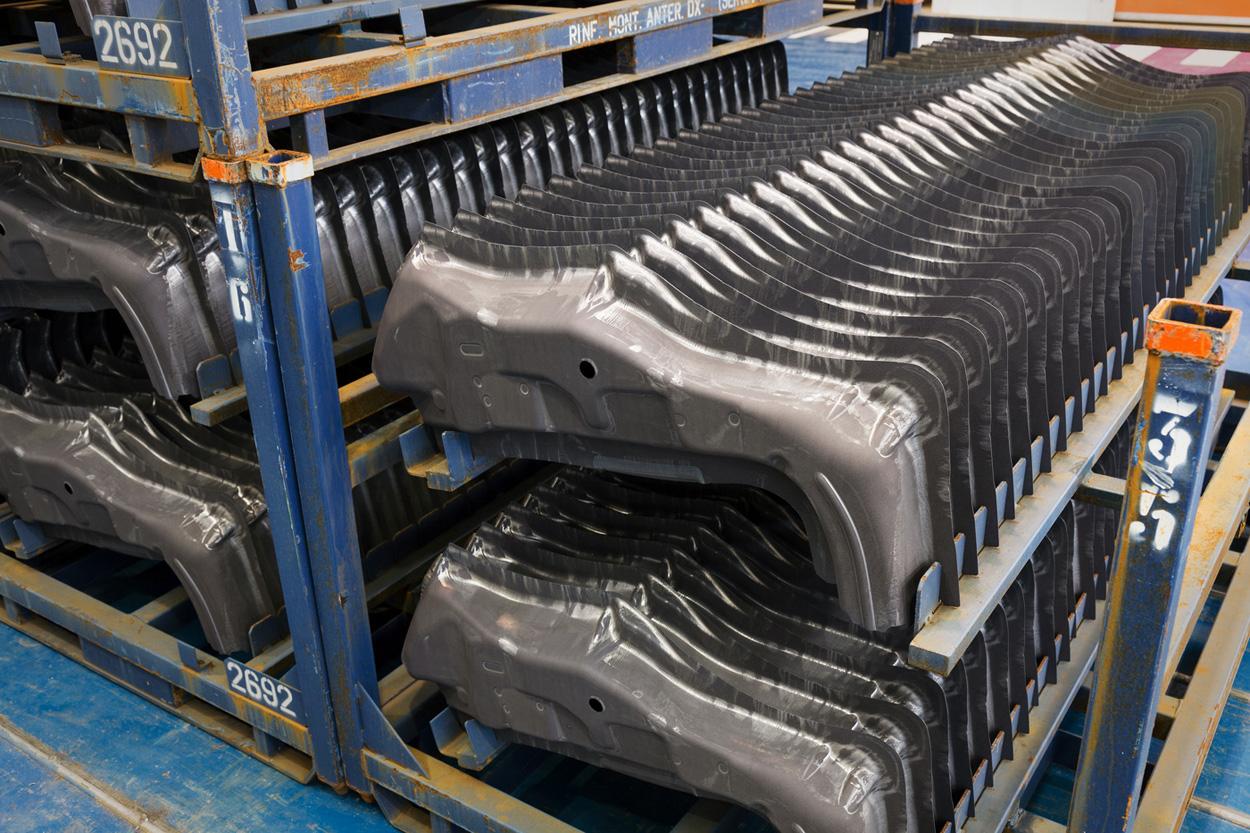