AP&T fully responsible for Aesculap’s new production line
Challenges are part of AP&T’s day-to-day operations, but some challenges are more complex than usual. The most recent assignment for Aesculap AG, which is located in Tuttlingen in southern Germany, undoubtedly falls into that category. “This is not like anything else I have ever been involved in,” says Kristian Broberg, who is the project manager in charge at AP&T.
As a leading player in a very unique market segment, Aesculap offers products and services for all surgical core processes from one single manufacturer: from opening and surgery to wound closure and sterile handling. The company needed a cooperation partner to build an automated press line. The aim was to increase and streamline the company’s production of what are known as sterile containers, which are metal containers used for sterilizing surgical instruments and other surgical equipment. In total, over fifty product variants made of aluminum or stainless steel are affected. A requirement was that it should be possible for all of the variants to be manufactured in one single line. AP&T was chosen to resolve the task after a careful selection process.

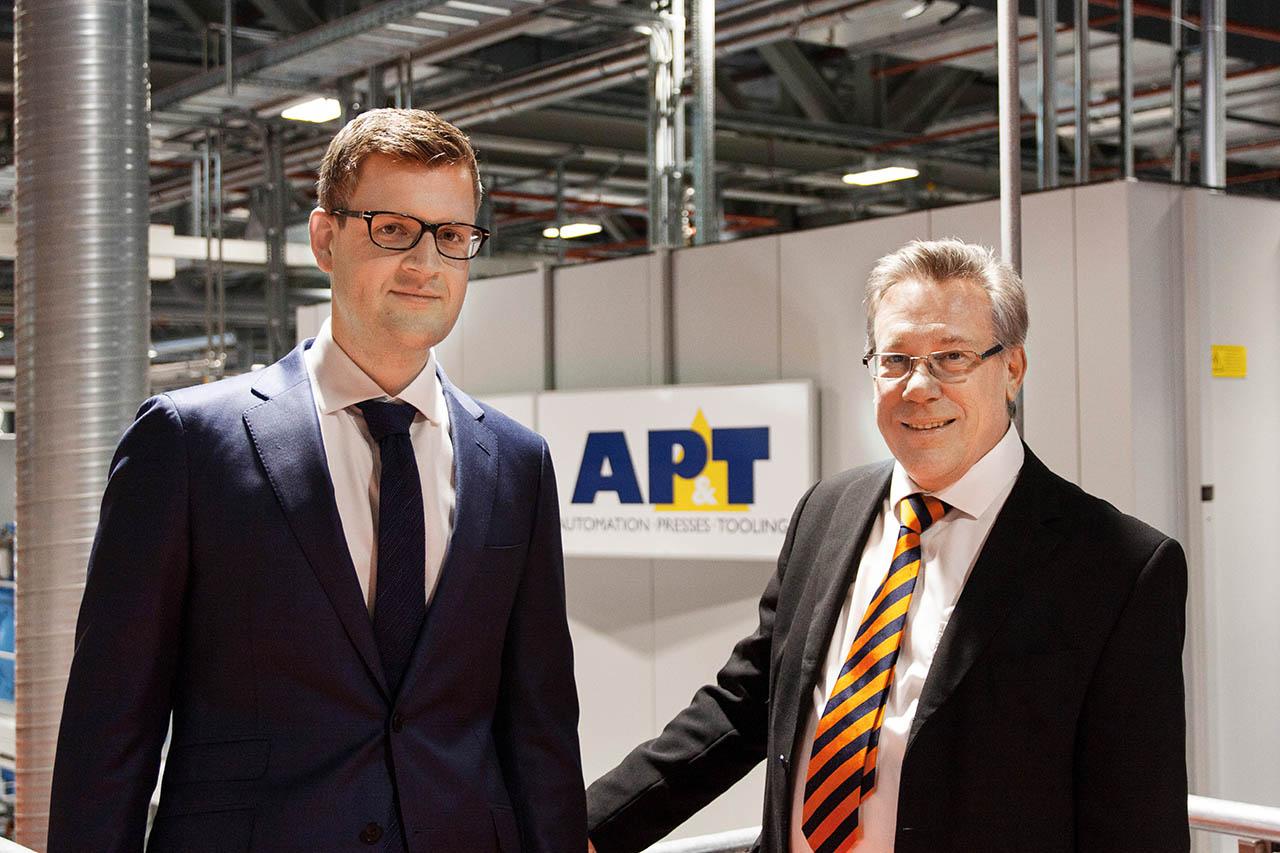
“AP&T presented a complete solution that corresponded to our requirements for flexibility in relation to different material flows and process control. AP&T was also willing to integrate and automate special purpose machines from other manufacturers in the complete installation,” says Markus Siller, segment head at Aesculap.
Before the procurement process was performed, detailed simulations of Aesculap’s planned production line and study visits to several of AP&T’s other customers in Germany, Denmark and Sweden were conducted in order to ensure secure project planning.
The majority of the new machines and all of the automation needed to build the production line were delivered by AP&T. An existing machine was also integrated, as was equipment from several other manufacturers. In its role as One Responsible Partner®, AP&T was tasked with integrating all of the included units so that they could be operated and controlled via a main control system. Manufacturing of the sterile containers comprises a large number of operations that must be matched with great precision to ensure that production proceeds smoothly and at a high rate. At the same time, it was also important to satisfy the requirement to be able to reset between different product variants quickly and easily. Another factor was that the production line, which consists of a total of eight presses and a large number of other machines and peripheral equipment, is divided into two parts, which did not make the task any less challenging.
“We had regular status reviews during the course of the project. During the decisive phases, we also had coordination meetings in a large group, where factory management and the strategic purchasing department took part to enable quick decisions. Installation was planned in the minutest detail to ensure the schedule. For example, all automation was set up and test run at AP&T in Sweden prior to delivery, which was an important prerequisite for preliminary approval,” says Markus Siller.
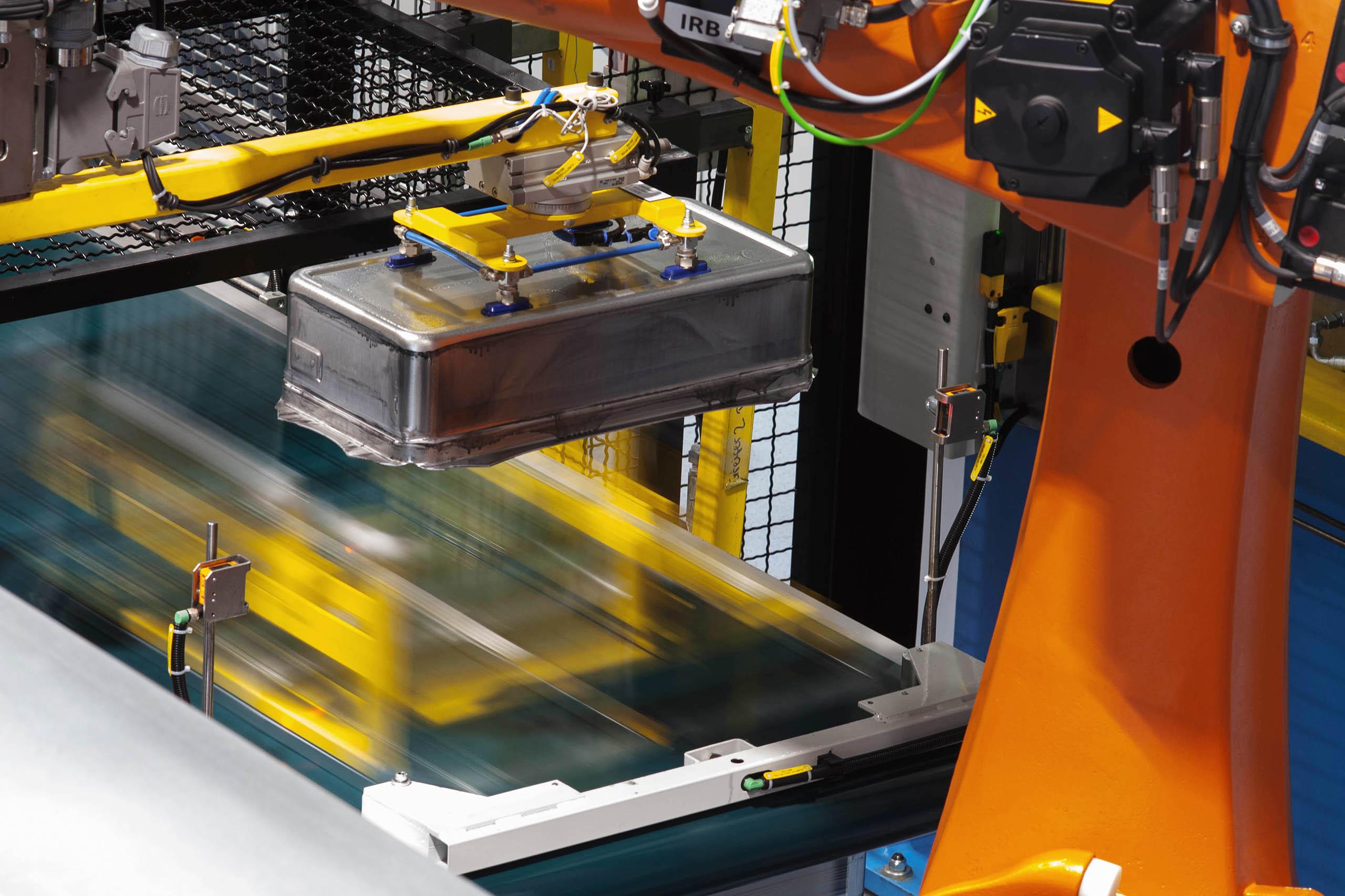
After a period of intensive work, the new line was in operation in October 2014, in conjunction with the inauguration of a new factory building at Aesculap’s facilities. Just over a year after the production start, experiences with the line have been very positive. Markus Siller says that the equipment was delivered completely in line with expectation.
“We are very satisfied. Thanks to the new line, we have been able to increase our capacity and satisfy the growing demand for our products. Increased automation allows us to meet demands for high quality and to improve our productivity at the same time.”
For AP&T, the project has provided new experience that can be used in future projects.
“This was a very interesting assignment where we truly had to live up to our promise of being One Responsible Partner®. We were responsible for control of all of the machines, all safety and all configuration. We also took care of the CE marking procedure for the entire production line. Despite the project's complexity, everything went very well – greatly attributable to very positive cooperation with Aesculap,” says Kristian Broberg.
May 2016
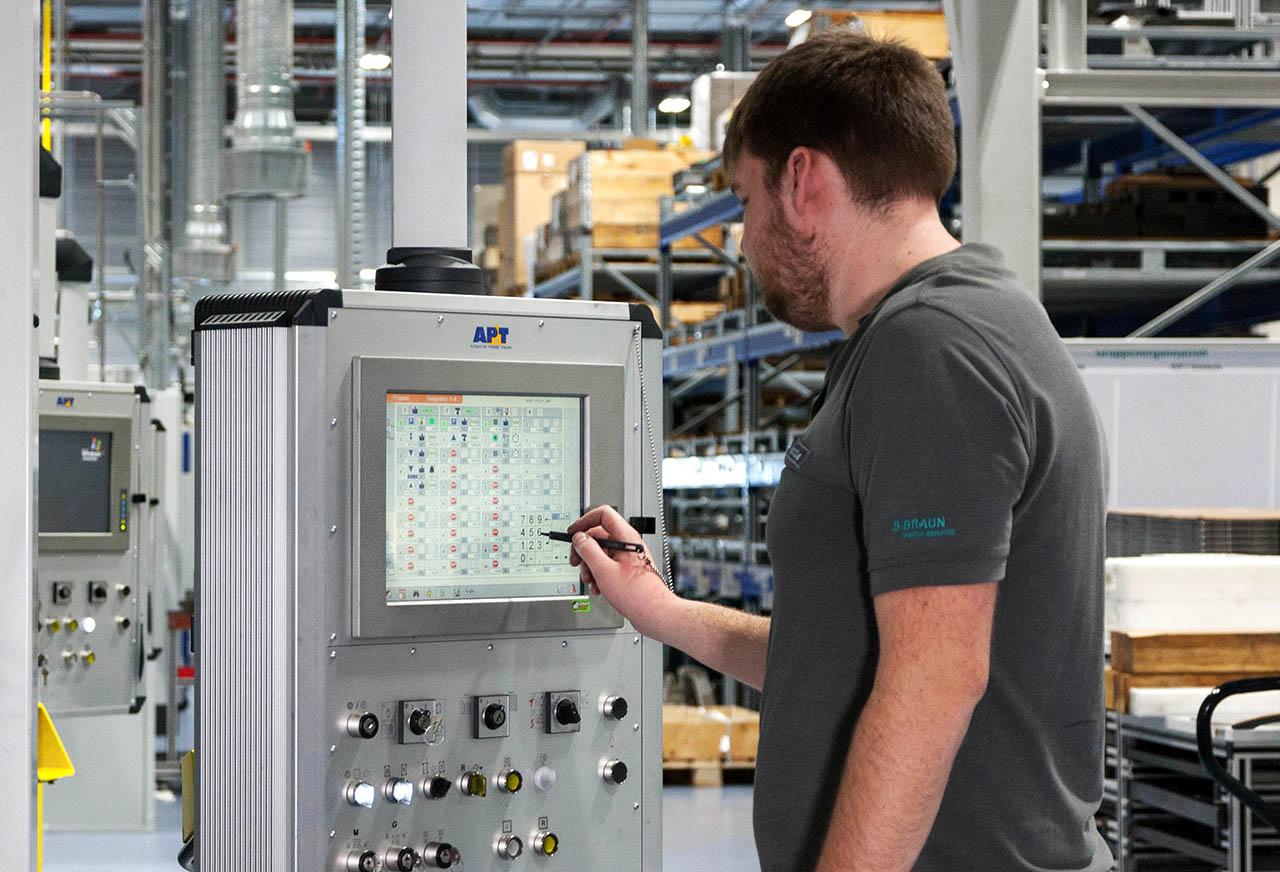
Facts about Aesculap
Aesculap is a division of B. Braun Melsungen AG, which is one of the world’s leading companies within medical and pharmaceutical devices. The company has 554,000 employees in 62 countries. Aesculap, with 11,500 employees, offers solutions within the following areas: general surgery, orthopedics/joint replacement, neurosurgery, laparoscopy, interventional vascular diagnostics and therapy, degenerative spine conditions and pulmonary vascular surgery. The company’s success is based on the ongoing knowledge exchange with customers, users and partners, and it has always had the same goal: to protect and improve the health of people all over the world.
Facts about the production line
The production line at Aesculap consists of four ODEN presses, a destacker, a SpeedFeeder, six industrial robots, mechanical shears, conveyors, positioning stations, gate protection and a complete control system. One existing press, three new presses from different manufacturers and special purpose machines are also included.